Off Duty
While the wind blew, the various research groups and the launch crew prepared and tested their experiments and rigs, like fishermen mending nets to get ready for the next big catch. At the end of each day we would check the wind conditions and then give up for the day, leaving the airport to seek dinner and retire to our rooms at the Super-8 for a few hours of personal time and sleep before repeating the routine the next day.
There were a number of restaurants we cycled through for lunch and dinner, trading off cost, convenience, and flavor. One of our favorites was a section of a local grocery store, Kessler’s, that hosted a small kitchen and some seating. It was run by a young Asian cook, and in addition to the usual menu items of sandwiches and fries, also offered stir-fried dishes with names we couldn’t pronounce but were utterly delicious. We thought it odd that the best Chinese food we had ever enjoyed was found inside a grocery store in this small South Dakota town.
On the weekends we would find things to entertain ourselves. There was the town’s movie theater showing “A Star Is Born” with Barbara Streisand. There were also local restaurants and bars that offered live music. I recall visiting one on a Saturday night where the musicians were playing country music, a genre I was aware of but did not have much exposure to. The characteristic rhythms, folksy ballads, and slide guitar licks were right at home in this place, and the audience was attentive and appreciative. But none were more enthusiastic than the Texan launch crew, who evidently had become regulars. They cheered and sang along with gusto, knowing the lyrics of every song and asking for their favorites. The band members loved them, but also seemed a little scared of them too.
Styrofoam insulation
The detectors within our instrument package needed to be held at a constant temperature during their operation. This was addressed in two ways: 1) internal heaters would keep the detectors at a target temperature, and 2) external insulation would slow the loss of heat from the instrument package to the extreme cold of the stratosphere. The better the insulation, the longer the heaters would last, and the more data could be collected.
One of my jobs was to craft an insulating exterior for the instrument. It was created from large blocks of styrofoam. But because the instrument was contained in a sealed cylindrical container with spherical endcaps, and with a “sidearm” to hold the spark chamber camera, it was a complex shape for which to make an insulation shroud.
This is where my freshman trigonometry course came to the rescue (once again). I was able to calculate the compound angles at which the blocks of styrofoam would meet without gaps as they wrapped around the cylinders. There were many pieces involved, each of which I numbered and mapped for its final assembly. I was gratified when I learned that, for the first time (compared to previous flights), they actually fit together and mated, minimizing the heat loss to space.
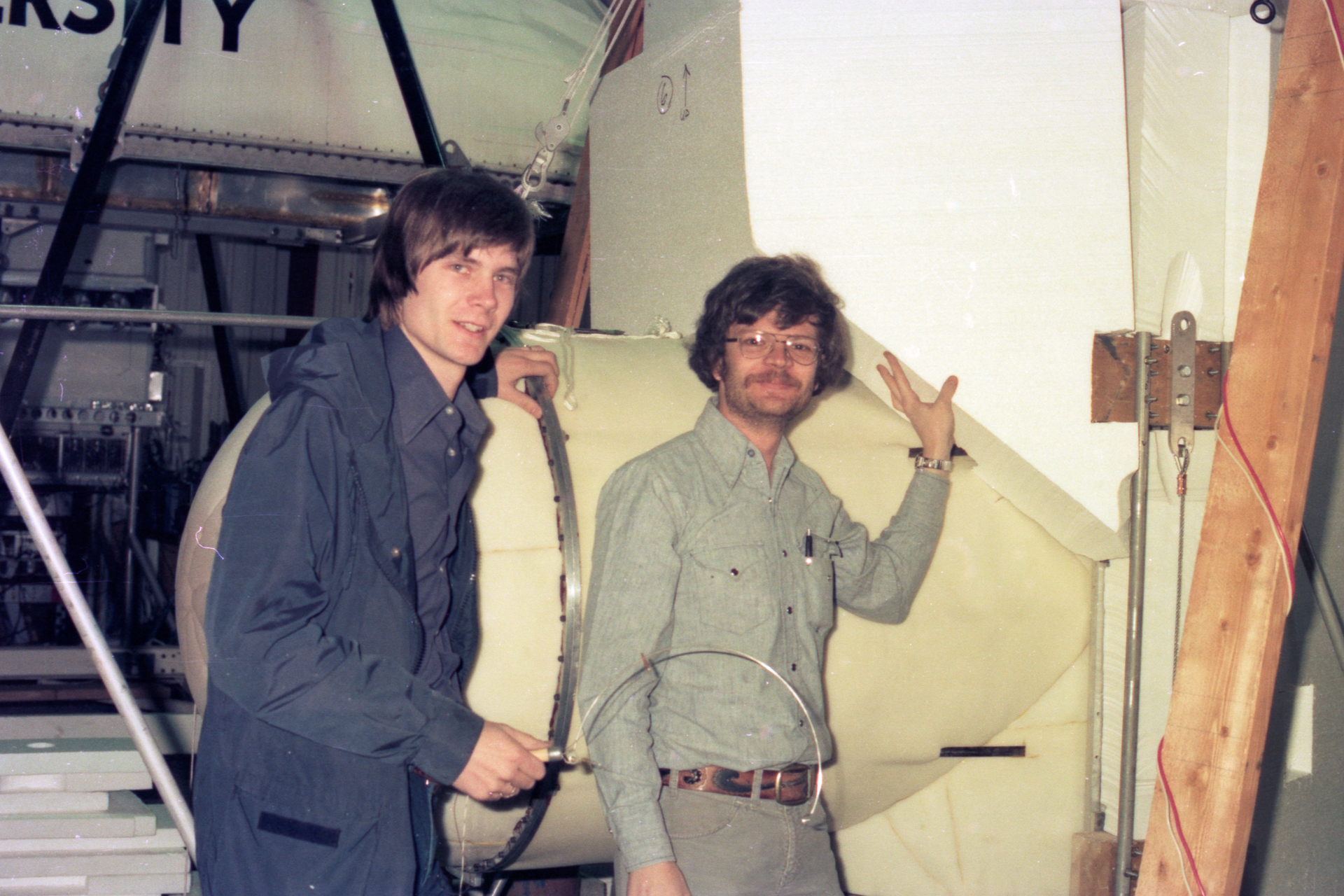
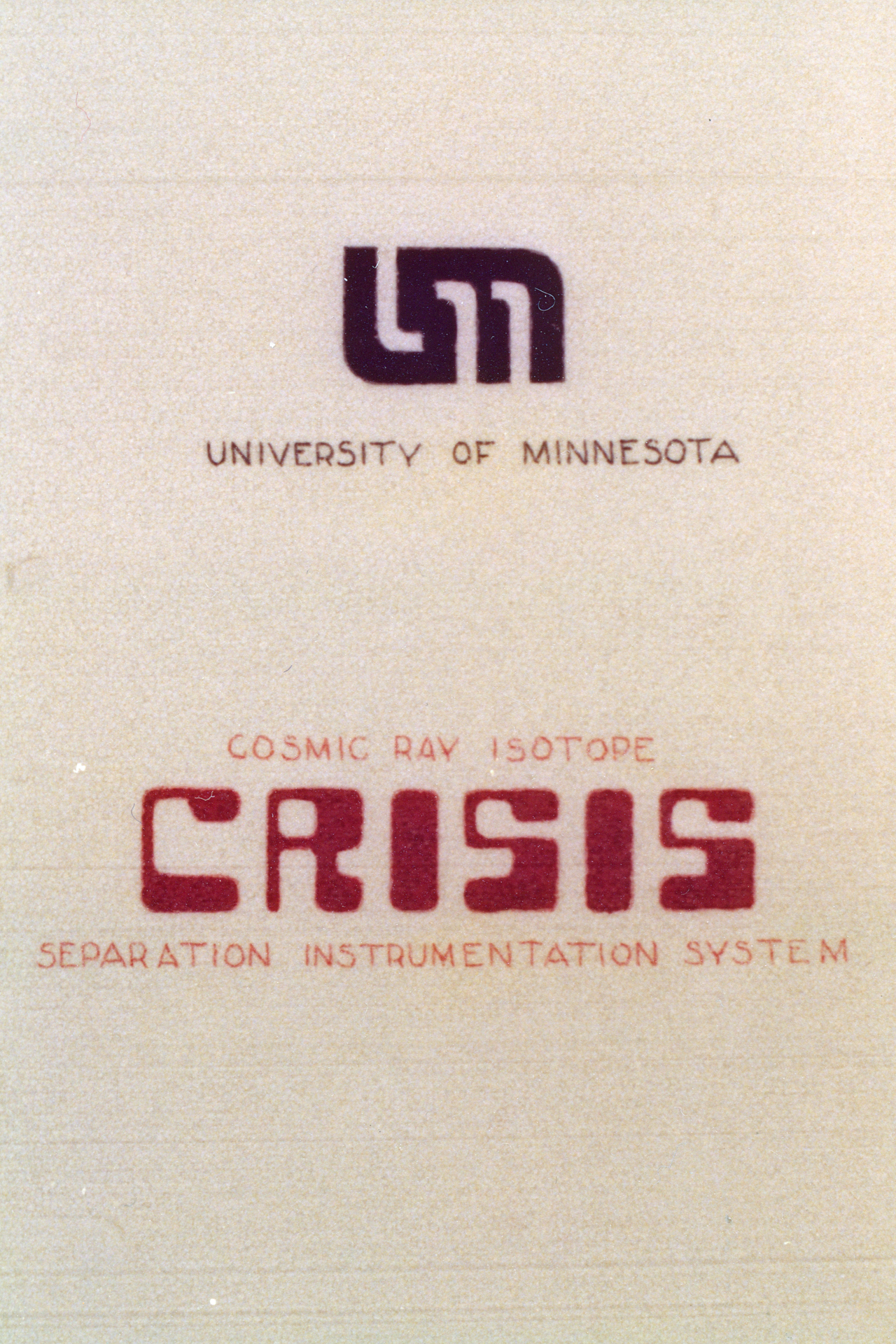
False Starts
Finally one day, the meteorologist declared that the winds would diminish in the late afternoon. We were skeptical, because it seemed like a day like every other—winds blowing across the prairie as usual. But sure enough, at around 5:00 the digital anemometer I had jury-rigged showed a leading zero for the first time in weeks.
It is a major commitment to initiate a balloon launch. The balloon itself is a specialized item, fabricated from panels of thin polyethylene plastic running hundreds of feet long, seamed together and then folded and packed carefully into a crate. Once opened and laid out on the tarmac for a launch, it could not be used for anything else. The integrity of the balloon skin was at risk if it were to be bundled back up and packed away for a later launch attempt. Nobody wanted a semi-used balloon to be hoisting their career-critical instrument package.
So decisions to launch were not made lightly. We heard stories from the Texas crew of launches gone wrong, where the weather was perfect right up until it wasn’t, with balloons twisting into self-damaging knots, or shearing to the side, unable to break free of the release spool, or splitting away from its helium filling tubes.
The Berkeley group was first in line to attempt a launch. Their superconducting magnet was readied, the balloon prepared and inflated, but something went wrong. My pictures of the effort show the balloon on the runway from afternoon until dark. The instrument was eventually disconnected and moved back to the hangar-lab. Later records indicate a balloon failure on the ground with no further detail.
Our group was now up for the next launch window which came a short time later. The package was prepared, hoisted from a crane, and moved into position, but the wind failed to die down as predicted. Fortunately the balloon remained in its crate and we remained on deck for the next launch opportunity.
The WUSTL group, alarmed after watching the failed Berkeley launch and our incomplete attempt, decided that maybe this was not the best time or place to launch their valuable instrument. They withdrew from their upcoming launch option, packed up, and went home.
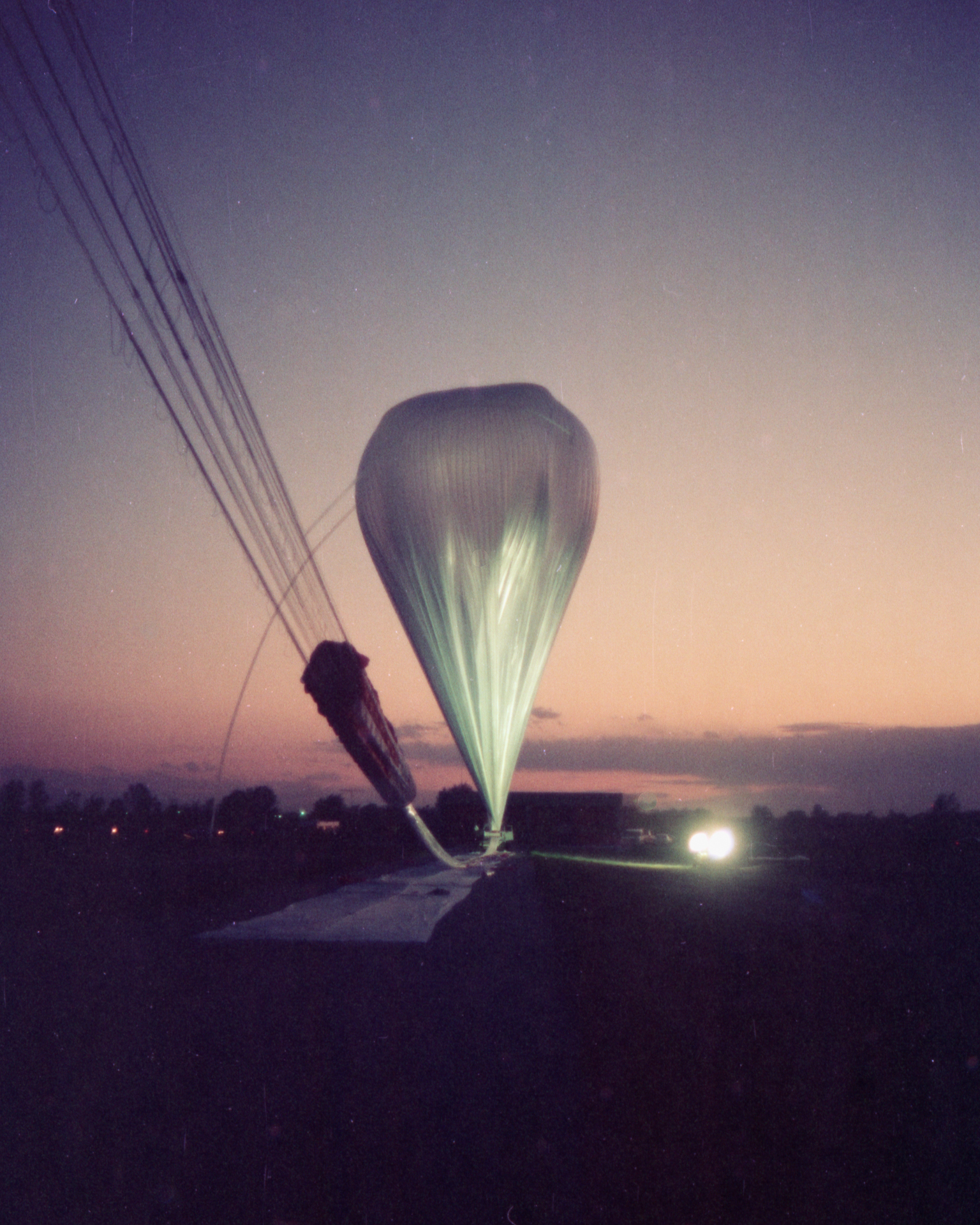